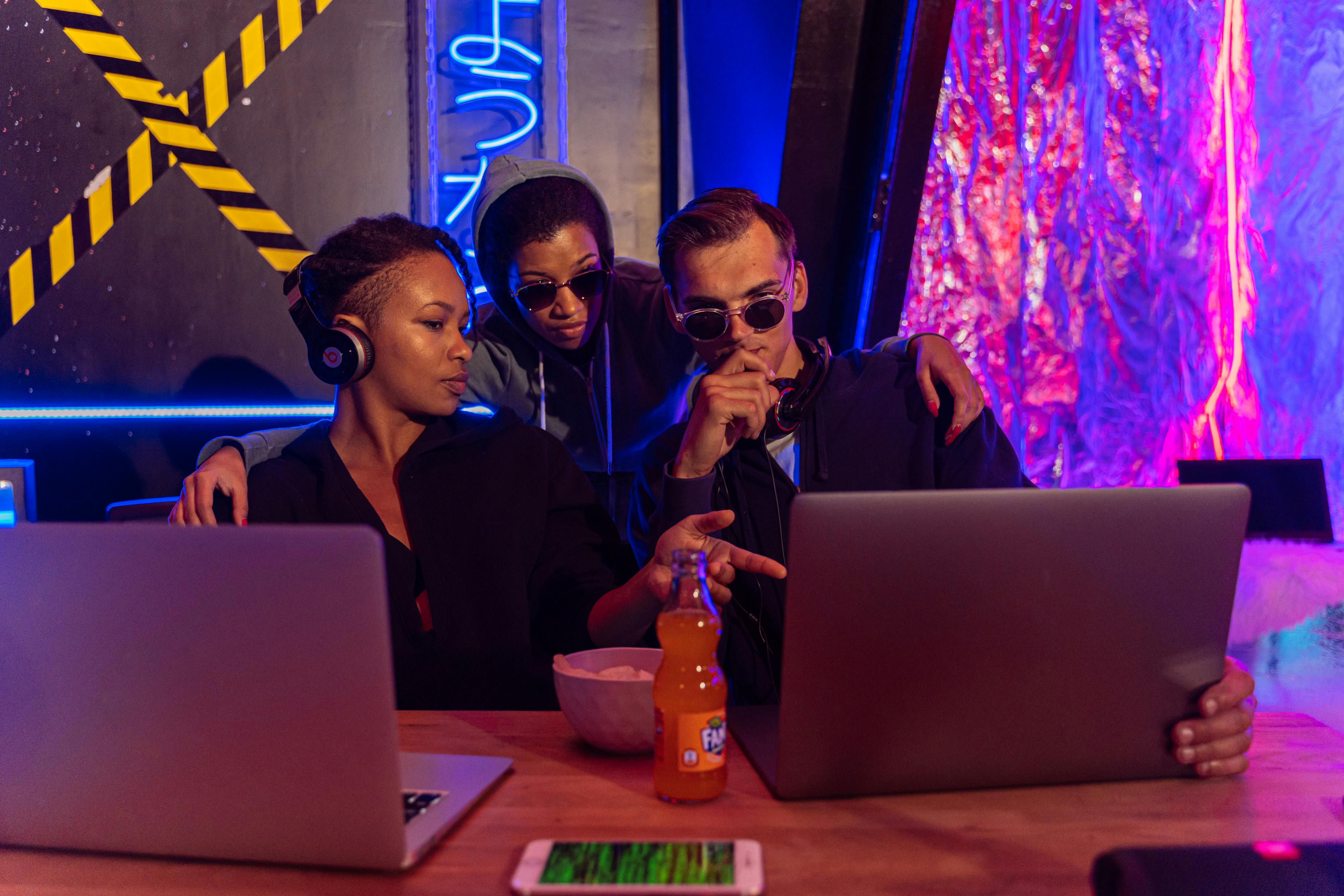
Metal Welding Pot – Tips on Tig Welding with HTS-2000, Aladdin 3-in-1, Gold Durafix
Welding metal pots isn’t as hard as people say, but it’s not as easy as you think…unless you know the tricks.
The metal pot is used for all sorts of cheap trinkets like figurines, cookie cutters, punch handles, and especially old car window crank handles. The problem with soldering this kind of thing is that sometimes the effort involved in soldering it isn’t worth it. But there are some things made of pot metal that are it’s worth fixing. Some that come to mind are antiques, old classic car parts like trim and trim, and Grandma’s old cookie cutter that is worthless but has sentimental value.
The pot metal is made of aluminum, zinc, copper, and possibly some other low-melting metals in various combinations. It is also known as die cast metal.
It is the zinc that makes welding difficult because zinc has a very low melting point and also tries to outgas when TIG welding. But it can be soldered with little trouble if you know how.
The 3 main welding rods are:
- HTS-2000
- Durafix
- Aladdin 3 in 1
These rods are advertised to be able to weld using just a small handheld propane torch. Actually, that’s brazing, not soldering, but the vendors at boat shows are really impressive when they patch big holes in beer cans.
But these zinc and aluminum welding rods can also be used for Tig Pot Metal welding.
If you are pretty decent at tig welding aluminum, you can surely read this article and do tig welding well too.
Usually potted metal parts are fairly clean, so only a little bit of grinding is required before welding. Usually the problem is that something just broke. If that is the case, a small groove in the crack will allow enough penetration for a strong bond. Remember, if it’s an ornamental piece and it breaks because someone dropped it, it will break again if dropped again, no matter how deep the weld goes, so take it easy on the penetration.
You need an A/C tig welding machine with high frequency starting. Most jobs can be welded with a small 1/16-inch tungsten electrode with a blunt cone on the tip. Set the amperage to only about 80 amps and you probably don’t even need that much.
Tig weld it like you would aluminum except you will only weld for about 5-10 seconds at a time before stopping to let it cool. Just when it starts to flow well. ARREST! It’s about to melt and fall into your lap. That’s the best advice for soldering these things.
Stop often and let cool.