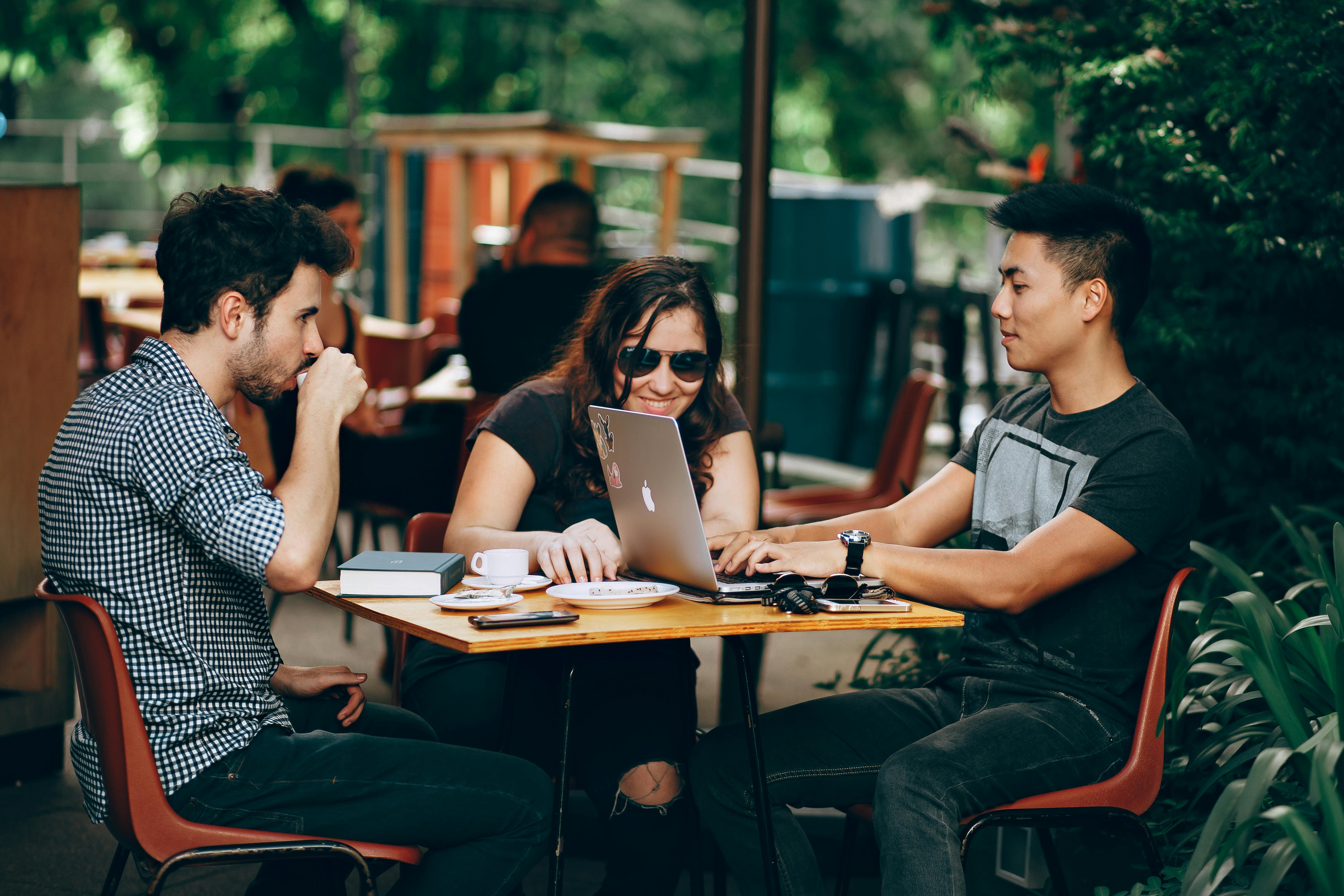
The history of industrial engineering
The Accreditation Board for Engineering and Technology defines industrial engineering as: the profession in which knowledge of the mathematical and natural sciences gained through study, experience, and practice is applied judiciously to develop ways of using economics, materials and the forces of nature for the benefit of humanity interested in the design, improvement and installation of integrated systems of people, materials, equipment and energy. It draws on specialized knowledge and skill in the mathematical, physical, and social sciences along with the principles and methods of engineering design and analysis to specify, predict, and evaluate the outcomes to be obtained from such systems.
History
The origins of industrial engineering can be traced back to many different sources. Fredrick Winslow Taylor is most often considered the father of industrial engineering, although all of his ideas were not original. Some of the earlier influences may have been Adam Smith, Thomas Malthus, David Ricardo, and John Stuart Mill. All of his works provided classical liberal explanations of the successes and limitations of the Industrial Revolution.
Another major contributor to the field was Charles W. Babbage. a math teacher. One of his major contributions to the field was his book On the economics of machinery and manufacturers in 1832. In this book, he discusses many different topics related to manufacturing, some of which will be very familiar to an IE. Babbage discusses the idea of the learning curve, the division of tasks and how learning is affected, and the effect of learning on the generation of waste.
At the end of the 19th century, more developments were carried out that would lead to the formalization of industrial engineering. Henry R. Towne emphasized the economic aspect of an engineer’s job. Towne belonged to the American Society of Mechanical Engineers (ASME), as did many other American pioneers in this new field. The IE handbook states: “ASME was the breeding ground for industrial engineering. Towne along with Fredrick A. Halsey worked on developing and submitting salary incentive plans to ASME. It was from these meetings that Halsey’s wage payment plan. The purpose was to increase worker productivity without negatively affecting the cost of production. The plan suggested that part of the profits be shared with employees. This is an early example of a pay-as-you-go plan of utilities.
Henry L. Gantt was a member of ASME and submitted papers to ASME on topics such as cost, worker selection, training, good incentive plans, and work scheduling. He is the creator of the Gantt chart, currently the most popular chart used in work scheduling.
What would Industrial Engineering be without mentioning Fredrick Winslow Taylor. Taylor is probably the best known of the pioneers of industrial engineering. His work, like others, covered topics such as the organization of work by management, the selection of workers, training and additional compensation for those individuals who could meet the standard developed by the company through its methods. .
The Gilbreths are credited with the development of time and motion studies. Frank Bunker Gilbreth and his wife, Dr. Lillian M. Gilbreth, worked on understanding fatigue, skill development, motion studies, and time studies. Lillian Gilbreth had a Ph.D. in psychology that helped her understand the problems of many people. One of the most significant things the Gilbrethss did was classify basic human movements into seventeen types, some effective and some ineffective. They labeled therbligs leaderboard. Effective therbligs are helpful in getting the job done and ineffective ones are not. Gilbreth concluded that the time to complete an effective therblig can be shortened, but it will be very difficult to remove. On the other hand, ineffective therbligs should be completely removed if possible.
In 1948, the American Institute of Industrial Engineers (AIIE) was first opened, beginning to bring professional authenticity to practicing engineers. Until that time, industrial engineers didn’t really have a specific place in a company’s hierarchy. The ASME was the only other society that required its members to have an engineering degree prior to the development of the AIIE.
What is the future of Industrial Engineers? With analytical methods and the advancement of computer technologies, the modeling of complex production and service systems will become more and more an everyday task.
Carrying out a motion study. Each job can be broken down into its fundamental job elements. The Gilbreth family discovered that there are seventeen such motions. The time to complete each move does not change. The works can be studied visually or with the help of a camera for micro-motion studies.
The environment for workers should also be established to promote work efficiency. Tools should be placed in fixed locations to eliminate search and selection therbligs. Work surfaces and chairs should be adjusted to the correct working heights to eliminate stress. Whenever possible, gravity feeders should be used to deliver parts to the correct location. Worker tools must be designed to eliminate multiple cuts. Adjustment handles should be designed to maximize the mechanical advantage of the operator.
Conducting a time study. Without a standard, it will be difficult for the company to estimate the delivery time of its products. Very big moments when the employee does not know what the expectation of the company is. To correct this problem, IE will develop a fair standard expectation for each operation. It has been estimated that 12% of a company’s total cost comes from direct labor. Another 43% of the cost comes from material cost. The other 45% is spent on general expenses. So the idea that the biggest productivity gains can be felt on the floor doesn’t hold up in this light. A good time study will take into account unavoidable delays, fatigue and, to some extent, outside interference. The time for useless steps, such as finding tools, will not be included in the final standard. The expectation is that the workplace is designed to accommodate the work and is free of this type of debris.
Installation times Setup time is the amount of time it takes to start producing different parts on a machine. If installation times remain long, the business will operate with high levels of work-in-progress and finished goods, tying up valuable business capital. Businesses that fail to reduce their lead times tend to appear slow to their customers.
cost An IE will generally be responsible for conducting a cost analysis on the equipment purchase. There are several ways to get to this. Life How long the machine is expected to last when performing the cost analysis.
Efficiency The traditional way of looking at efficiency was to keep the machine running at 100%. The idea was that the cost of the machine could be spread over the amount of time it was kept running. The higher the machines efficiency, uptime/available time, the better the accounting numbers for the cost of the machine.
material The IE deals with the delivery and flow of material throughout the plant, often the plant has evolved as the company has.
Lot Size To allow the manufacturer to remain flexible, production lot sizes should be minimized. This will only be economical after the reduction of machine configurations has been achieved.
inventory levels Since inventory is capital that cannot be converted until a consumer finishes and buys it, it should be kept to a minimum. Inventories not only tie up capital, but if the customer requests a change, the inventory risks becoming obsolete.
Quality The quality of the material can affect all parts of the system. Poor quality material often introduces excessive amounts of rework into each of the processes. A typical job for an IE would be to work with the quality department to establish a QMS quality management system.
Maintenance The amount of maintenance that the machine will require is a variable to take into account. Another issue about maintenance is whether or not the available staff will need to be trained.